Non sarà una rivoluzione, ma è certamente un bel cambiamento. Se non altro, perché aggiunge un’ulteriore infornata di elettronica su macchine già parecchio dotate, in questo senso. Stiamo parlando delle nuove Case Axial Flow 250, le mietitrebbie – assiali, ovviamente – del marchio di casa Cnh, che a nove anni dal lancio, subiscono un ammodernamento piuttosto radicale, per certi aspetti. Come l’introduzione di un sistema di taratura automatica dei parametri di raccolta. Grazie al quale, assicura il costruttore, un operatore inesperto può aumentare la produttività fino al 10% e uno già navigato può fare lo stesso lavoro con meno fatica.
Presentate in piena estate a Dresda, le nuove Axial Flow saranno in produzione dall’autunno, giusto in tempo per essere nei campi a primavera 2019. Tre i modelli: 7250, 8250 e 9250, per potenze da 498 a 634 cv. Prendono il posto delle già performanti AF 240, lanciate nel 2015. Scopriamo in cosa le migliorano.
Elettronica
in primo piano
Tocca, ancora una volta, partire dall’elettronica. Né del resto la cosa deve stupire, se analizziamo cosa è stato cambiato sulle assiali di Case Ih.
L’aspetto più di rilievo, anche nelle parole del costruttore, è infatti il sistema Afs Harvest Command, ovvero il software che automatizza le più comuni impostazioni della mietitrebbia, ma anche la velocità di avanzamento della stessa. Agendo su giri del rotore e posizione delle alette, volume dell’aria e apertura dei crivelli, il sistema è in grado di adattarsi da solo alle mutate condizioni del prodotto. Non secondo uno schema fisso, ma in base a quattro diverse modalità di lavoro che vedremo in seguito.
Il sistema è modulare, vale a dire che si può attivare su diversi livelli (anche di prezzo, ovviamente). Quello di base regola giri del controbattitore e ventilazione in rapporto al prodotto che si sta raccogliendo ed è attualmente disponibile per grano, mais, soia e colza. Il passaggio successivo prevede la gestione automatica della velocità di avanzamento in base alla quantità di prodotto e funziona con qualsiasi coltura. L’operatore imposta la massima velocità e il carico del motore, esattamente come si fa per i trattori, dopodiché lascia al software la gestione della macchina. Tre le opzioni possibili: massima resa, controllo delle perdite o resa produttiva fissa.
Del tutto nuovo, e sulla carta davvero avanzato, il livello più alto di automazione: in questo caso il sistema elettronico interviene, come abbiamo visto, anche sulla posizione delle alette e sui giri del battitore, oltre che su crivello e – novità della serie 250 – precrivello, che diventa registrabile anche dalla cabina. Quattro, come scritto sopra, le modalità di lavoro: massima resa, resa costante, qualità della granella e modalità bilanciata (una media tra le tre precedenti, a quanto capiamo).
Sedici sensori
La gestione automatica delle impostazioni è resa possibile da una rete di sensori che monitora costantemente sia le prestazioni della macchina sia le condizioni della raccolta. Il più importante di essi, secondo Case Ih, è la telecamera multispettrale (luce ultravioletta, verde, blu, rossa e infrarossa) collocata sul canale elevatore della granella: un dispositivo che analizza in tempo reale il prodotto, alla ricerca di materiale diverso (leggi pula e altri inquinanti) ma anche di amido, indice di rottura della granella. Grazie alle informazioni trasmesse dalla telecamera, Afs Harvest è in grado di intervenire sui parametri di raccolta, ottimizzandoli.
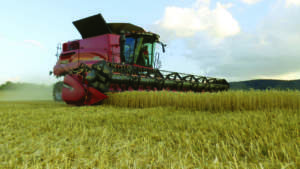
Assai interessante, inoltre, il sensore di carico collocato sul cassone crivellante. Serve sia a livellare il medesimo in pendenza (fino al 12% di dislivello trasversale) sia a prevenire le perdite, adeguando ventilazione e posizione dei crivelli quando il carico di prodotto è eccessivamente sbilanciato. Grazie a questi sensori, precisa Case Ih, il sistema distingue tra perdite per eccesso di carico o per eccesso di ventilazione ed è particolarmente efficace nei momenti di passaggio, come le svolte a fine campo o l’arresto della macchina durante la raccolta.
Interventi
sulla meccanica
Come abbiamo scritto in precedenza, pur essendo preponderante, la componente elettronica non è la sola su cui i progettisti siano intervenuti. Partendo dall’alimentazione, una delle innovazioni principali riguarda il canale elevatore, potenziato nel sistema di sollevamento per lavorare agevolmente con le grandi barre richieste dalla capacità operativa della 9250. Con i nuovi martinetti, fa sapere Case Ih, le Axial Flow hanno il 18% di alzata in più e possono sollevare fino a 6,1 tonnellate, sufficienti per gestire una 14 metri da grano o una 18 file per il mais. Hanno anche un doppio sistema di correzione dell’inclinazione laterale, sempre per le barre extralarge. Infine, un sistema di adattamento frontale (optional) permette di variare l’inclinazione della barra anche di 12 gradi.
Invariato, sostanzialmente, il reparto di trebbiatura, mentre migliora lo scarico del prodotto, portato a 113 litri al secondo, e soprattutto il sistema di trinciatura dei residui. Per il quale al cliente è lasciata la scelta tra versione tradizionale e Xtra Chopping, in grado di spargere la pula su una superficie larga 12 metri.
Ultima, ma non meno importante, la trasmissione, ora basata su due marce meccaniche e un motore idraulico a due velocità, che permettono all’operatore di selezionare tra opzione campo e strada (rispettivamente, 18 e 40 km/h) e di cambiare tra prima e seconda marcia all’interno di ciascuna di esse. Grazie a questo sistema, le Axial Flow possono superare pendenze stradali fino al 36%. L’adozione di dischi dei freni interni raffreddati a olio migliora infine la capacità di arresto.
Tanta elettronica, come si vede, e poca meccanica nelle novità di una serie che da sempre fa vanto del rispetto del prodotto e della notevole capacità di raccolta. E che si avvicina sempre più a gestire uno e l’altra in piena autonomia.
SI SCOMMETTE SUL TRAFFICO CONTROLLATO
Ridurre al minimo il compattamento del terreno può portare grossi benefici in termini di fertilità e produzione. Forte di questo assunto, Case Ih si sta impegnando nella sensibilizzazione dei clienti sull’importanza di contenere il più possibile i passaggi in campo. O, quantomeno, di concentrarli in poche precise scie.
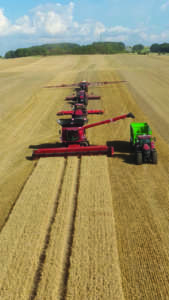
È il principio del traffico controllato o meglio gestito. Perché, come ha spiegato lo specialista dell’agricoltura di precisione Ian Beecher-Jones, non in tutte le operazioni e non con tutte le colture è possibile passare sempre negli stessi punti. «L’importante – ha precisato – è che in ogni singola operazione i passaggi siano ridotti al minimo e il più possibile concentrati».
Per attuare la gestione delle tracce è praticamente indispensabile lavorare con guida automatica, possibilmente a livello Rtk. Dal prossimo anno, fa sapere Case Ih, essa sarà disponibile non soltanto in campo, ma anche nelle svolte, grazie al sistema Accuturn Pro, che si affianca alla guida automatica Accuguide. Premendo un solo pulsante l’operatore potrà così avviare la memoria di fine campo e svoltare esattamente sulle tracce dell’anno precedente, minimizzando il compattamento del terreno in capezzagna, oltre che in campo.