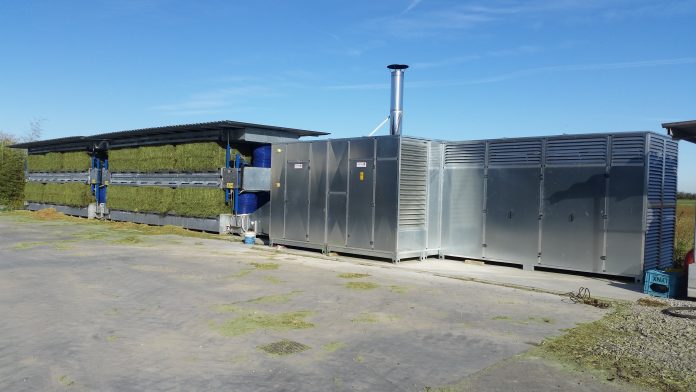
Questo tipo di processo prevede l'impiego di specifici impianti che possono essere realizzati in opera o in lamiera e, in questo caso, operano appoggiati su un’area pavimentata. In entrambi i casi è utile proteggerli con tettoie di una certa ampiezza per poter gestire con tranquillità le operazioni di carico e scarico anche in caso di pioggia. La gestione dell'impianto è infatti diversa rispetto a quella per il foraggio sciolto perché in questo caso la cella è anche il luogo fisico in cui avviene la conservazione, mentre nel caso del foraggio imballato al termine dell'essiccazione il prodotto è asportato dall’impianto e immagazzinato nei fienili. Pertanto, al termine del processo, le balle sono asportate dalla platea rendendo possibile l'inizio di un nuovo ciclo di essiccazione.
La platea di questi impianti ha un sedime rettangolare ed è costituita da una camera di ventilazione dotata di fori di ventilazione sui quali sono deposte le balle. Su uno dei lati corti è inserito un ventilatore, che è sempre di tipo centrifugo, e un generatore di calore.
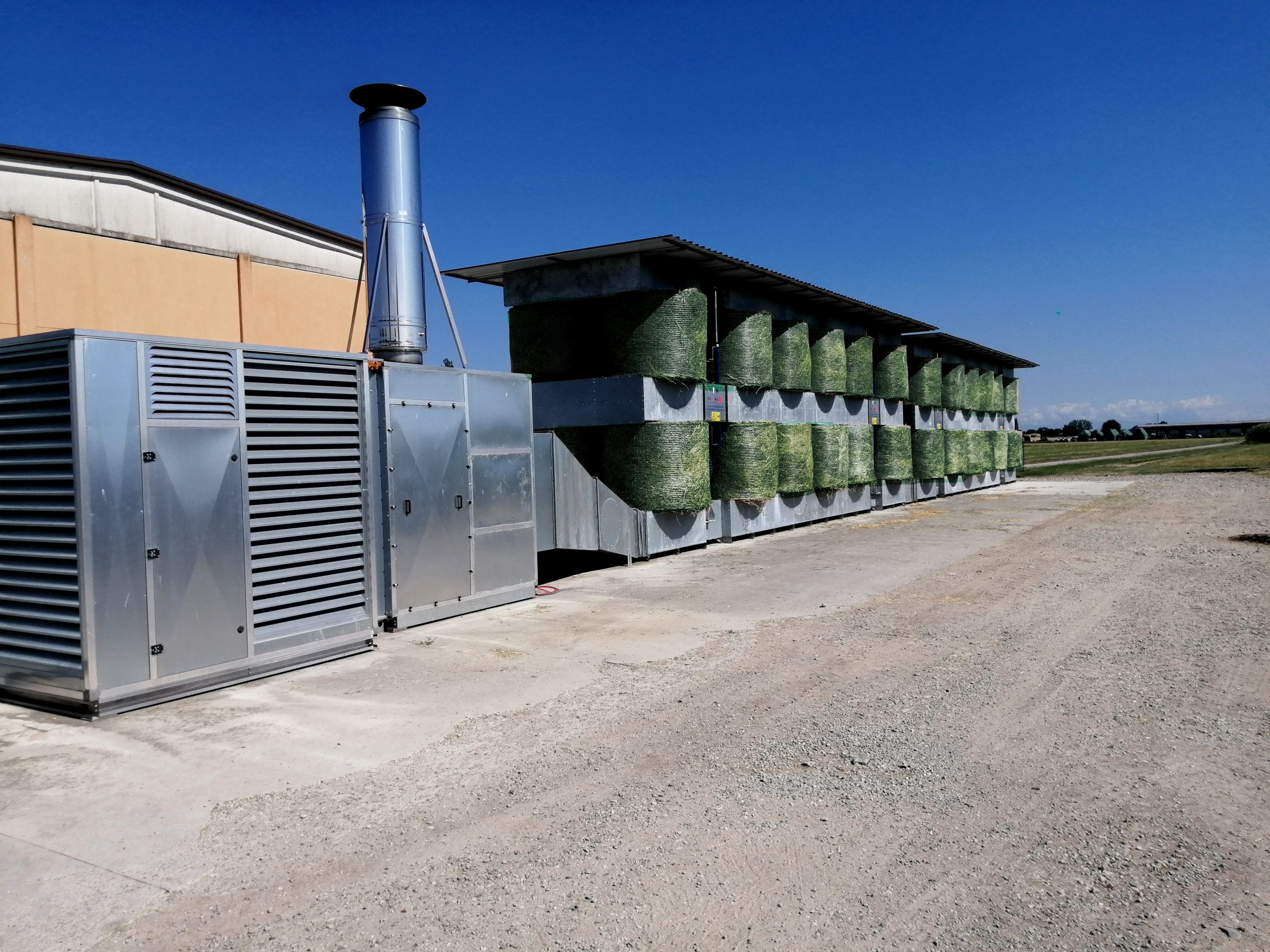
La camera di ventilazione
Negli impianti in opera la camera di ventilazione è realizzata in calcestruzzo armato sormontata da una platea costituita da piastre prefabbricate, di forma quadrata o rettangolare, ciascuna delle quali dotata di un foro in posizione centrale sul quale viene depositata la balla. La platea così è formata è transitabile da trattore. Negli impianti in lamiera il carico è realizzato mantenendo il caricatore telescopico o il trattore dotato di caricatore frontale all’esterno dell’impianto; per questo motivo le balle sono spesso disposte solo su due file.
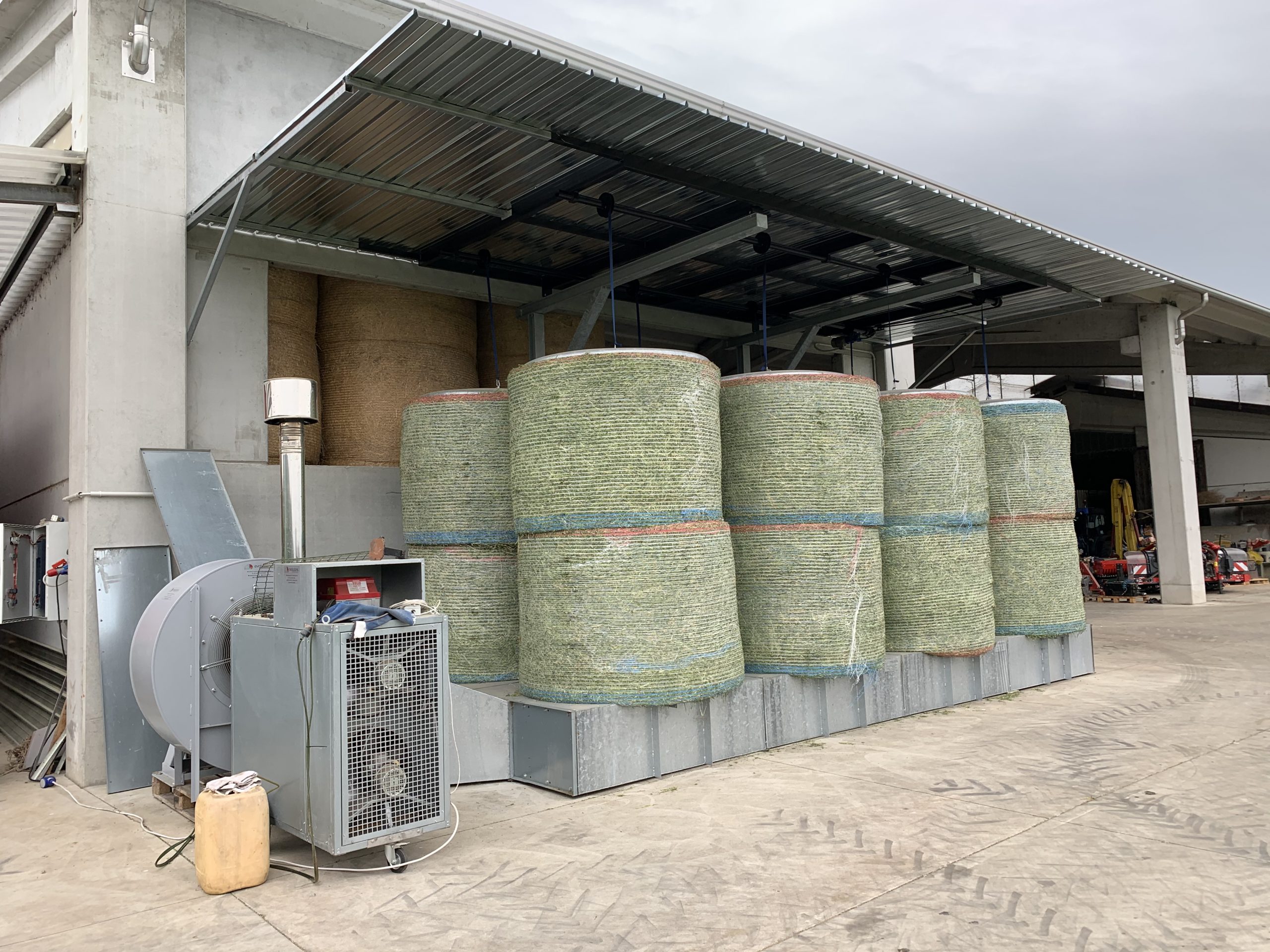
La luce libera all’interno della camera di ventilazione deve essere la maggiore possibile. Indicativamente è bene non sia inferiore al 40-50 cm per garantire alla massa d’aria ventilata di espandersi, equalizzarsi e quindi defluire attraversando il foraggio evitando ulteriori perdite di carico. Indicativamente un buon rapporto fra la portata d’aria dell’impianto, espressa in m3/s, e il volume della camera di ventilazione, espressa in m3, dovrebbe risultare inferiore a 0,6 Hz, con valori ottimali inferiori a 0,5 Hz. Tuttavia vi è molta variabilità sotto questo aspetto. Gli impianti con flusso d’aria contrapposto, ossia quando l’aria raggiunge la balla sia dal basso sia dall’alto, sono muniti di due camere di ventilazione in comunicazione fra loro. La sezione di questi collegamenti e in generale di tutte le condotte dell’aria deve essere tale da non causare un innalzamento delle perdite di carico che determinano la pressione di esercizio dell’impianto. Anche il canale di raccordo fra ventilatore e camera di ventilazione deve essere caratterizzato da una sezione che aumenta di dimensione allontanandosi dalla bocca di uscita del ventilatore.
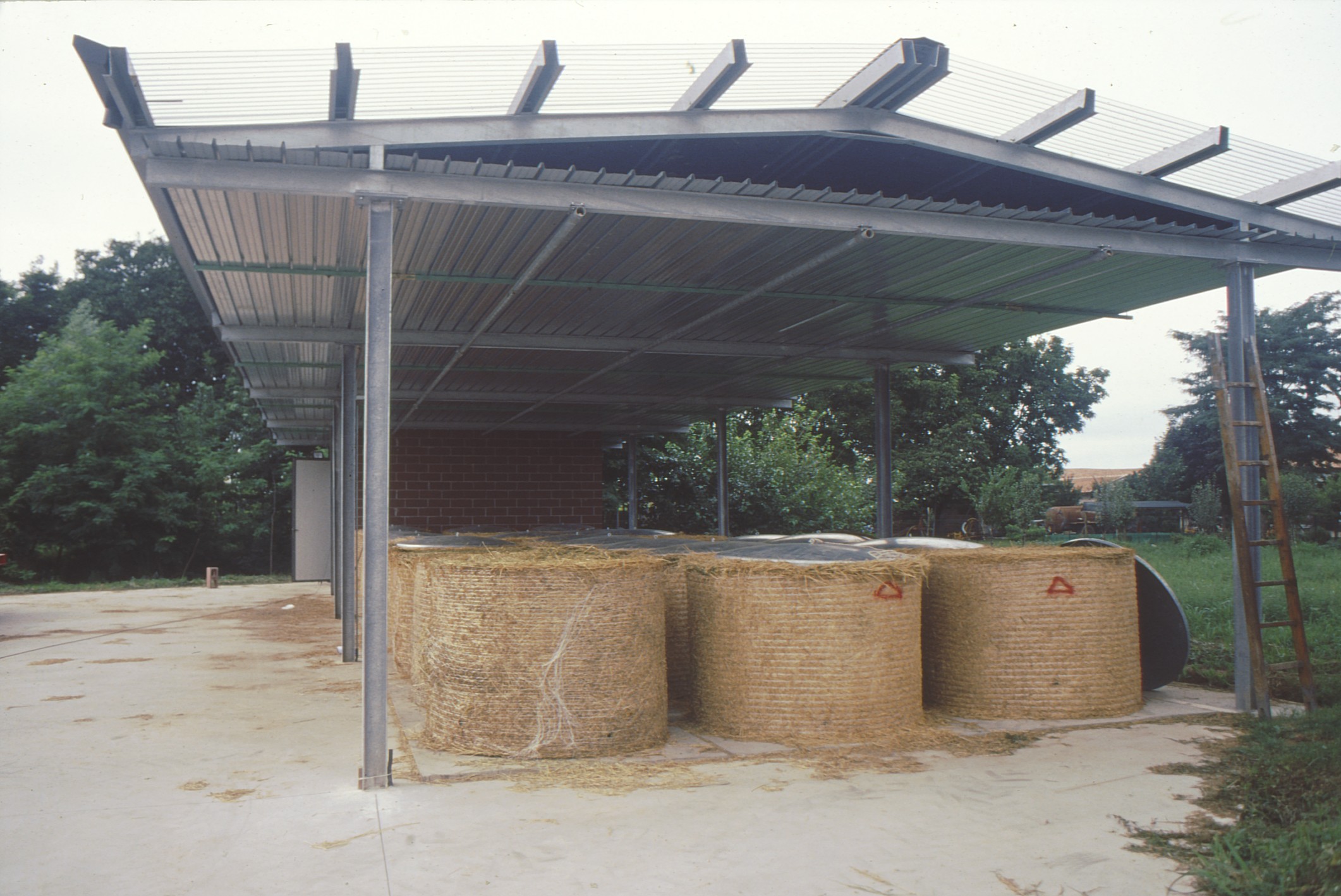
Qualche dato tecnico
La compressione della rotoballa, determinata con l'imballatura, oppone però una maggiore resistenza al movimento dell'aria rispetto al foraggio sciolto; questo fatto comporta l'aumento della pressione di esercizio, in particolare all'inizio del processo di ventilazione in cui si possono rilevare valori di pressione totale compresi fra 500 e 1.200 Pa (circa 50 e 120 mm di colonna d'acqua). In queste condizioni si possono instaurare, nell'area di contatto fra la rotoballa e la piastra, delle vie preferenziali di uscita attraverso le quali l'aria ritorna all'ambiente senza attraversare il foraggio. Per evitare questa perdita, che incide negativamente sul bilancio energetico del processo, vengono adottati alcuni accorgimenti in grado di migliorare la tenuta fra la base della rotoballa e la piastra di appoggio. Un equilibrato rapporto fra il diametro del foro della piastra e quello della rotoballa, compreso generalmente fra 0,6 e 0,7, unito alla realizzazione lungo il bordo del foro della piastra di particolari rilievi, consente di ridurre l'entità di questo fenomeno. Va ricordato che un rapporto maggiore tende a incrementare le perdite d'aria, mentre la riduzione, in termini assoluti, del diametro del foro causa un aumento della pressione di esercizio.
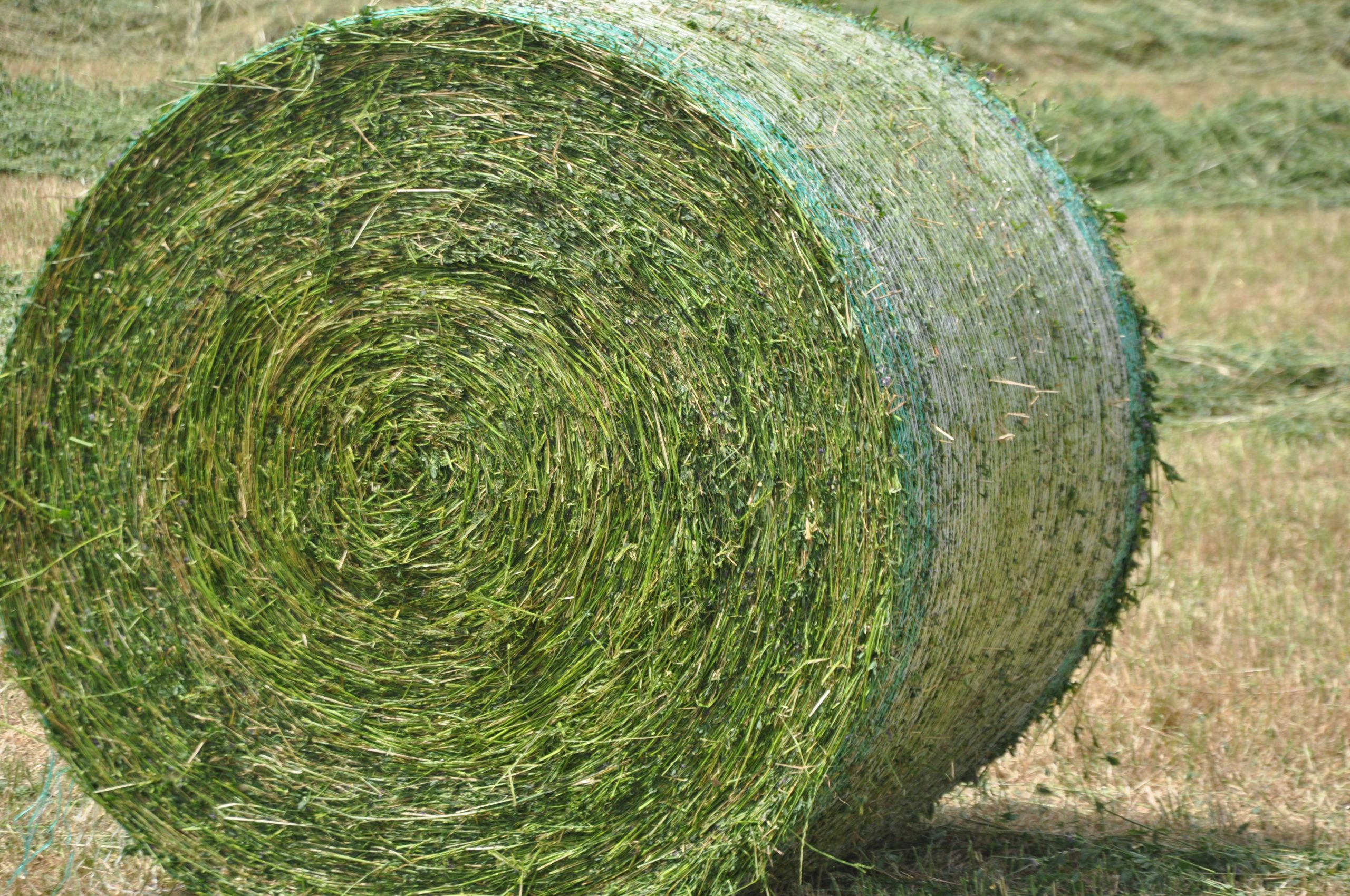
Indicativamente il ventilatore centrifugo di un impianto a bassa temperatura è in genere dimensionato per garantire una portata di aria compresa fra 0,6 e 0,7 m3/s per foro di ventilazione alla pressione di esercizio di 500 Pa con balle di oltre 2 m3 di volume. La potenza elettrica installata per la ventilazione risulta pari a 0,6-1,2 kW per foro di ventilazione e circa tre volte maggiore per motori endotermici tipo Diesel.
I tempi di permanenza sull'impianto variano in funzione delle condizioni di temperatura e umidità dell'aria di ventilazione, del contenuto di umidità del foraggio e dell'uniformità con cui viene distribuita l'aria all'interno della rotoballa. Possono ridursi notevolmente riscaldando l’aria di ventilazione; già con 6-8°C in più rispetto alla temperatura ambiente la durata del processo tende a dimezzarsi.
Gli impianti che prevedono l’uso di generatori di calore solo in caso di necessità sono caratterizzati da una più lunga permanenza del foraggio sull’impianto, ma anche da un più basso consumo energetico. Per migliorare le prestazioni dell’impianto mantenendo basso i consumi è conveniente realizzare pannelli solari aria-aria. Quando i canali di raccordo fra pannello e ventilatore sono ben dimensionati i pannelli solari contribuiscono in modo molto efficace al processo di ventilazione.
Nei casi in cui vi siano degli impedimenti tecnici o economici nella fornitura di energia elettrica alcun e aziende agricole hanno installato motori diesel. In questo caso è interessante utilizzare parte del calore prodotto dal motore che è in grado di incrementare la temperatura dell’aria ventilata di circa un grado che equivale a circa 4 punti percentuali di umidità relativa (ovviamente la riduzione del valore di umidità relativa dipende dalle condizioni di partenza).
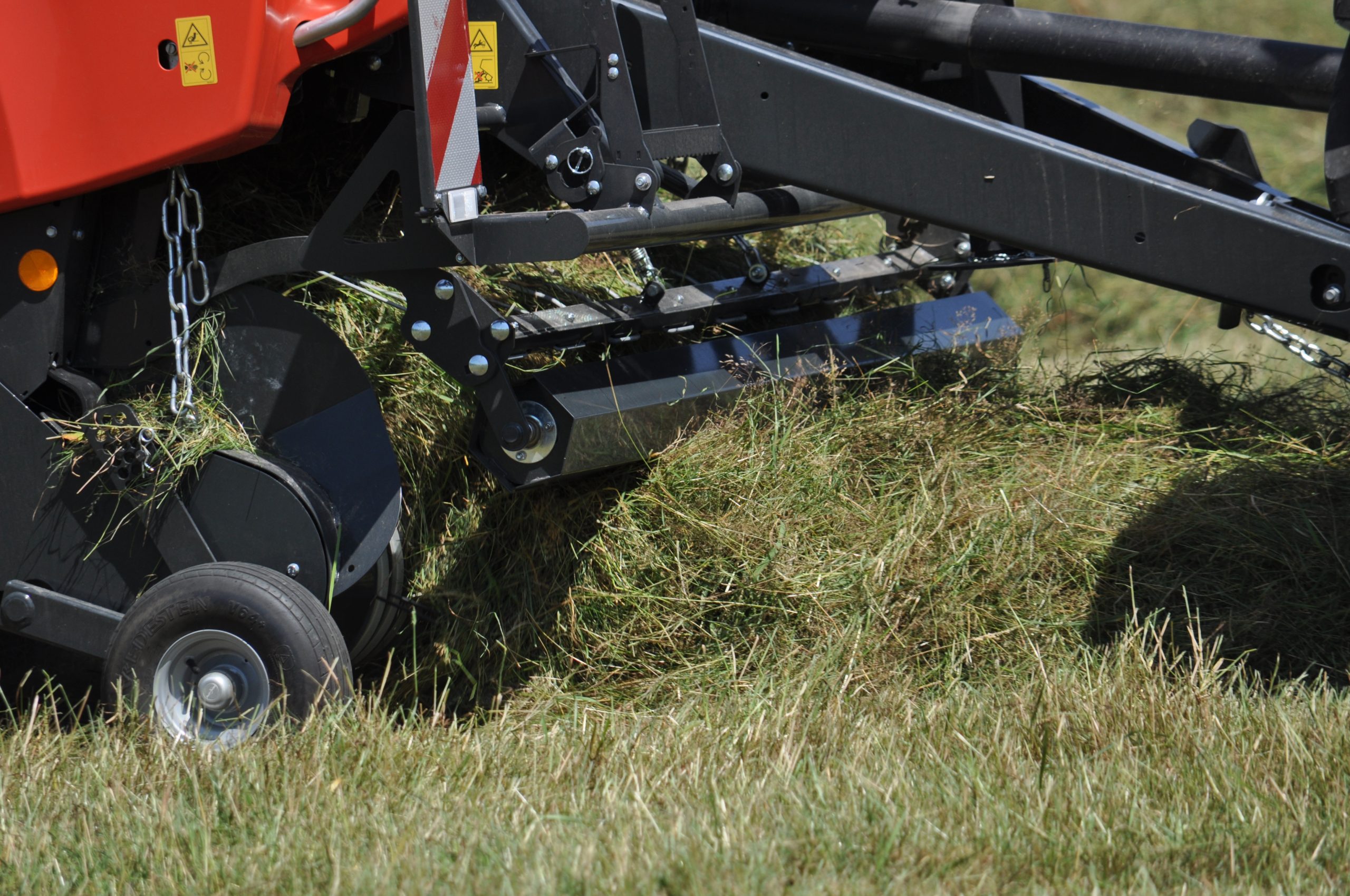
A causa del maggior volume e della non sempre ordinata distribuzione del foraggio al suo interno il processo di essiccazione all'interno della rotoballa può presentare delle difficoltà aggiuntive rispetto alle balle prismatiche. Infatti, con le rotoballe l’essiccazione può risultare meno uniforme perché è più lenta in quei settori in cui minore è il flusso dell'aria. Ciò si verifica per la presenza di zone in cui il foraggio ha una maggiore densità e, in modo evidente, questo fenomeno si manifesta nello strato più esterno delle rotoballe realizzate con rotoimballatrici a camera di compressione a volume costante. L'applicazione di particolari coperture da porre sulla base superiore delle rotoballe, la sovrapposizione di due balle, l’adozione di impianti a flussi contrapposti favoriscono la diffusione dell'aria in tutta la rotoballa favorendo il completamento dell'essiccazione del foraggio situato in posizione più esterna.
Tuttavia contribuisce a migliorare l’efficienza del processo realizzare rotoballe con una distribuzione più uniforme del foraggio, come sono quelle ottenute con rotoimballatrici a camera di compressione variabile. Va però posta attenzione a non realizzare rotoballe troppo dense e pesanti, soprattutto con foraggi di prato stabile o ricchi di graminacee. Quindi è necessario disporre di imballatrici sulle quali sia possibile modificare la compressione esercitata sul foraggio: questa deve ridursi al crescere del contenuto di umidità. La permeabilità all'aria della rotoballa è infatti correlata con la sua massa volumica che può essere modificata al momento della raccolta agendo sui dispositivi di regolazione presenti sulle imballatrici.
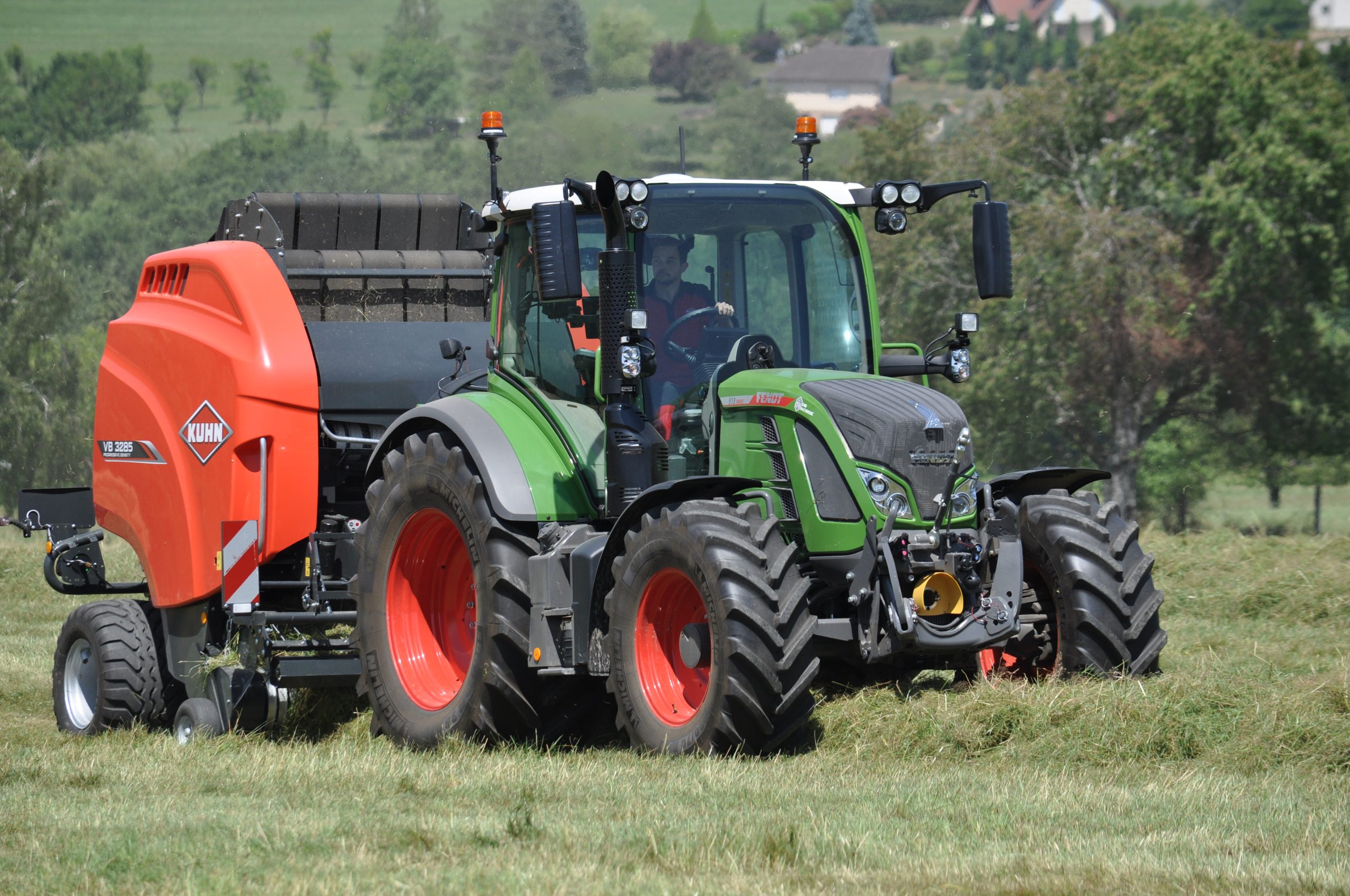
Consumo energetico
Stabilire a priori il consumo energetico è complesso proprio perché è difficile valutare gli aspetti che sostanzialmente dipendono dall’umidità di raccolta del foraggio e dalle condizioni di processo. Negli impianti che operano con incrementi termici ridotti (indicativamente massimo 10°C), fra i fattori che influiscono sulla spesa energetica vanno annoverati la portata d’aria, la naturale capacità essiccante dell’aria e la modifica della temperatura dell’aria ventilata.
In modo particolare per la tipologia destinata all’essiccazione del foraggio imballato (proprio perché opera in modo discontinuo), conviene sfruttare la naturale capacità essiccante dell’aria e i sistemi di generazione del calore passivi quali il collettore solare ad aria e la cogenerazione, riservando l’intervento del generatore di calore a situazioni di effettiva necessità. Di fatto l’impiego del generatore d’aria calda o di qualsiasi altro apparecchio energivoro destinato a modificare i parametri psicrometrici dell’aria dovrà essere azionato solo in presenza di umidità relative dell’aria vicine al punto di equilibrio igroscopico.
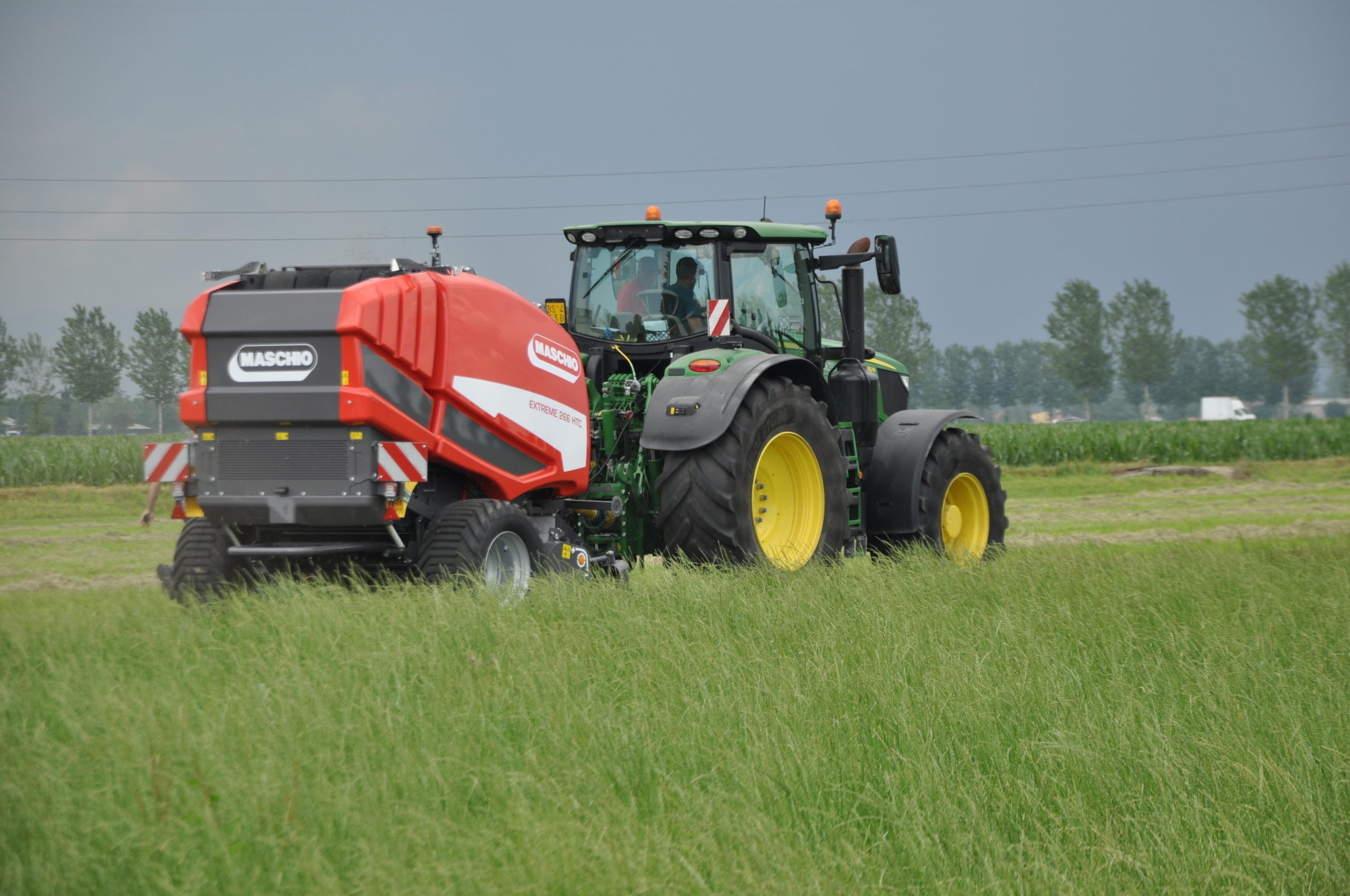
Infatti, se esaminiamo il comportamento energetico di un razionale impianto per l’essiccazione delle balle si può facilmente determinare la notevole differenza che sussiste fra il consumo di energia utilizzata dal ventilatore e quella per riscaldare l’aria. La prima raramente supera valori di 1 kWh (elettrico) per rotoballa (meno per le balle prismatiche), mentre la seconda è generalmente compresa fra i 4 e gli 8 kWh (termico) per rotoballa, rispettivamente con un salto termico di 5 o 10°C. È comunque possibile (e necessario!) razionalizzare la ventilazione ed in particolare l’uso del generatore di calore anche attraverso sistemi automatici che provvedano in base ai parametri termo igrometrici rilevati condurre le opportune regolazioni.
Quando il ventilatore è azionato da un motore elettrico attraverso la semplice adozione di un timer è possibile ridurre la ventilazione durante le ore più umide (ad esempio quelle notturne) adottando dei cicli di ventilazione che consentano di evitare i problemi di rialzo termico nel foraggio. Questa tecnica va però adottata con cautela soprattutto quando il foraggio tende a riscaldarsi con facilità.
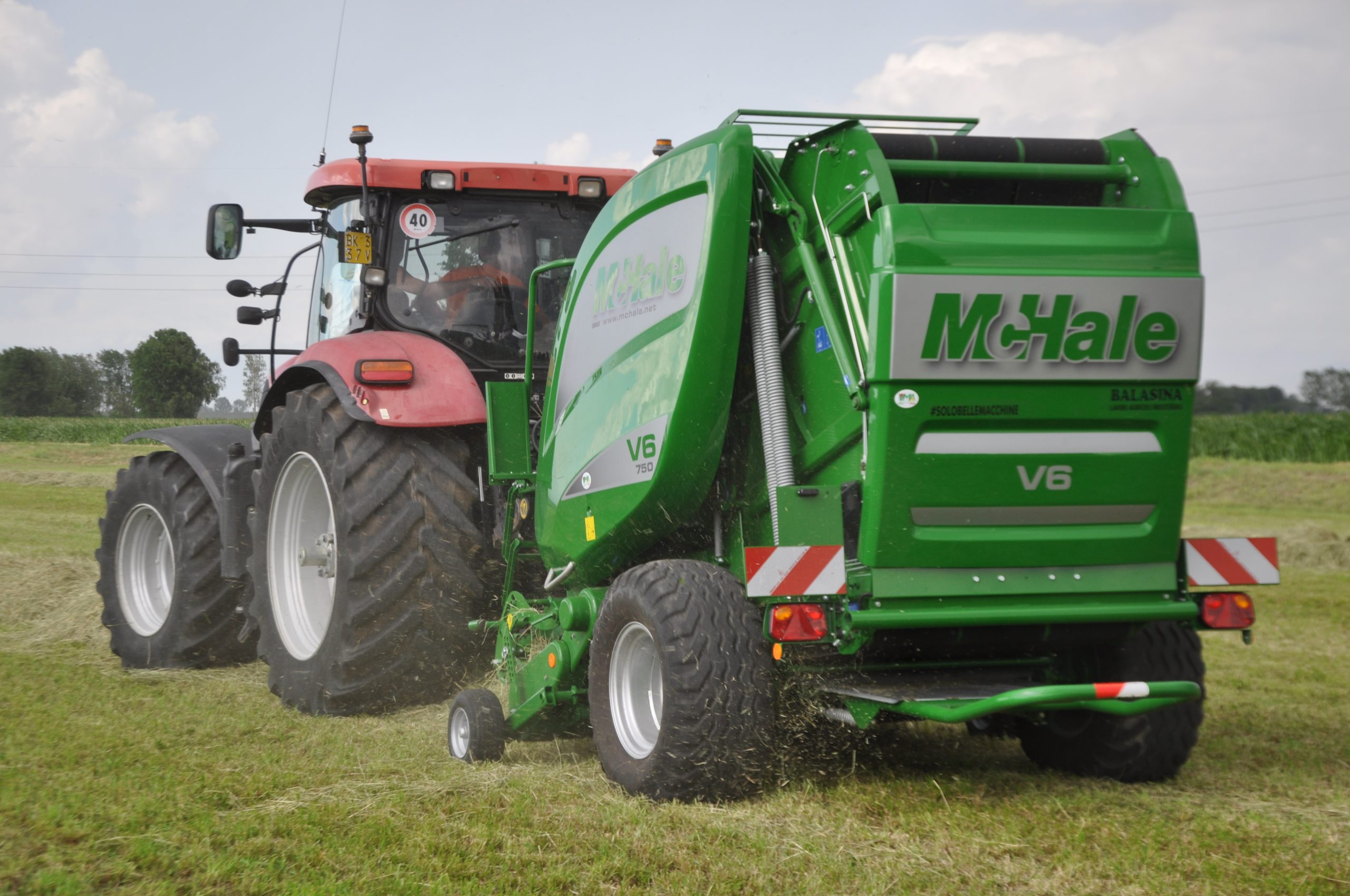
Riduzione della spesa energetica
La riduzione della spesa energetica può essere conseguita anche utilizzando fonti energetiche alternative a quelle fossili. Infatti, gli impianti sono sempre dotati di generatori di calore, alimentati a gasolio o ad altri combustibili fossili, in grado di produrre un incremento termico che non dovrebbe essere superiore agli 8-10°C, dato che l’incremento della temperatura di esercizio comporta una riduzione dell’efficienza dell’essiccazione che si ripercuote negativamente sui costi del processo.
I bruciatori a combustibili fossili possono essere sostituiti da apparecchi predisposti per lo sfruttamento delle biomasse provenienti dall’agricoltura, dalle lavorazioni forestali, dalle segherie e dall’industria del legno. La loro convenienza è però fortemente condizionata dall’andamento del mercato o dalle effettive possibilità di procurarsi la biomassa direttamente.
Nel dimensionamento di questi sistemi di riscaldamento bisogna considerare che per innalzare di un grado un metro cubo d’aria sono mediamente necessari non più di 1,25 kJ e che, pertanto, i consumi di biomassa saranno indicativamente compresi fra 1,3 e 2,6 kg/h/foro di ventilazione mentre quelli di gasolio si attestano fra i 0,44 e i 0,88 kg/h/foro. Il rapporto fra la resa energetica fra biomassa legnosa e gasolio è quindi pari a 3:1.
Fra le fonti energetiche integrative per il riscaldamento dell'aria la più affidabile e diffusa in questo settore è però quella basata sul recupero della radiazione solare mediante collettori solari ad aria, realizzabili anche in economia, una volta individuata la corretta soluzione tecnica.