Moda o sostanza? Cosa c’è dietro l’innegabile, evidente successo delle barre a tappeti? Perché chi sta acquistando una mietitrebbia sopra i 400 cavalli la prende regolarmente in considerazione, talvolta prima ancora di valutare una tradizionale testata a coclea? Cercheremo di capirlo nelle prossime pagine.
Il dubbio viene anche soltanto parlando con i contoterzisti, quelli che hanno comprato una trebbia di alta potenza, negli ultimi tre-quattro anni, l’hanno abbinata a una barra a tappeti o hanno pensato di farlo. E se non l’hanno fatto, probabilmente se ne sono pentiti. Per una verifica, abbiamo chiesto ai costruttori di mietitrebbie, ottenendo piena conferma: le quote di mercato delle barre a tappeti, rigide o articolate (altrimenti dette, impropriamente, flessibili), sono in costante ascesa. Stando a un nostro rapido sondaggio, di tutte le testate vendute una su due è tradizionale, per il resto sono barre “alternative”. Flessibili, a tappeti, a fondo variabile. Tutto, insomma, tranne che comuni barre da grano.
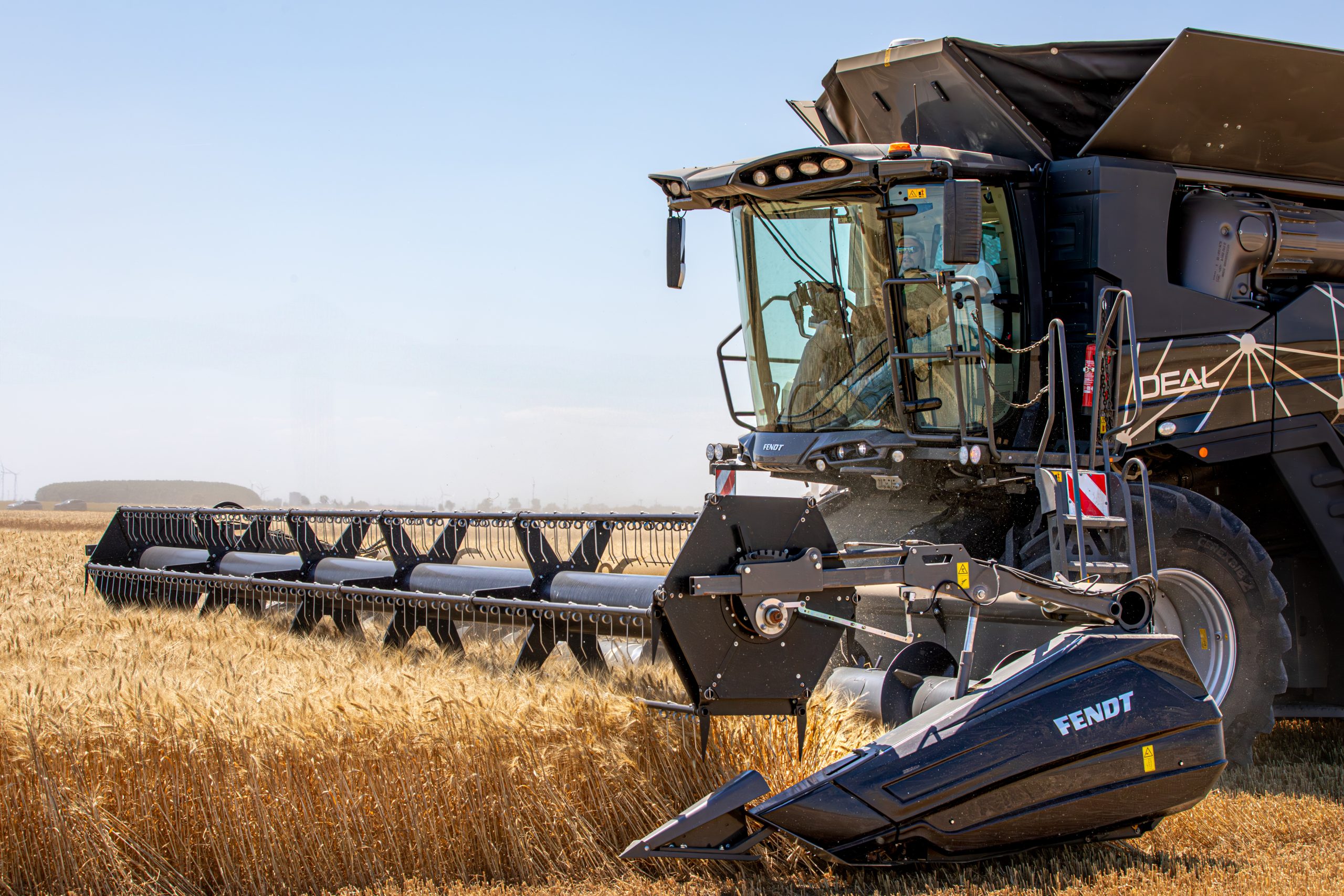
La Powerflow, qui in foto, appartiene infatti alla classe delle barre ibride, con tappeti trasversali e coclea per il trasporto del prodotto
Le differenze con quelle tradizionali
Trovandoci su una rivista dedicata ai contoterzisti, tralasciamo i dettagli sul funzionamento della barra a tappeti, ben noti ai nostri lettori. Ci concentriamo invece sulle differenze tra quest’ultima e le testate tradizionali. La più evidente è il sistema di trasporto del prodotto: coclea per le convenzionali, due tappeti laterali più uno centrale per le “nuove” barre a tappeti (nuove si fa per dire, essendo in circolazione ormai da oltre trent’anni). È però ciò che non si vede, più di ciò che si vede, ad attirare l’attenzione dei possibili acquirenti. A iniziare dal funzionamento: le barre a tappeti raccolgono il prodotto in modo molto più ordinato rispetto alle testate tradizionali e lo convogliano sul tappeto centrale, che lo porta al canale elevatore. Le piante, dicono in molti, arrivano all’elevazione con la spiga rivolta in avanti e dunque entrano nel battitore o nei rotori nelle migliori condizioni per una sgranatura veloce e indolore. Opinione non condivisa da tutti, dal momento che sul tappeto centrale, e poi all’ingresso del canale, gli steli subiscono bruschi cambi di direzione e non è affatto detto che continuino a essere così ordinati come sui tappeti laterali.
Non ci sono invece dubbi sull’uniformità di alimentazione. La barra a tappeti invia agli organi di trebbiatura e separazione un flusso costante di prodotto, che non ha picchi né buchi come accade spesso, invece, con la coclea. La quale trasporta il materiale verso il canale elevatore in modo disomogeneo, dando luogo al caratteristico avanzamento alternato, tipico delle mietitrebbie di qualche decennio fa, quando le barre e il sistema di separazione non erano certo quelli odierni.
L’alimentazione uniforme è assicurata inoltre dalla possibilità di regolare a piacere la velocità dei tappeti. A muoverli sono infatti motori idraulici, sui quali l’operatore può facilmente agire tramite un comando posto in cabina. Può dunque aumentare o ridurre il ritmo di trasferimento del prodotto in funzione della quantità presente in campo e del bisogno di evitare intasamenti a livello di canale elevatore.
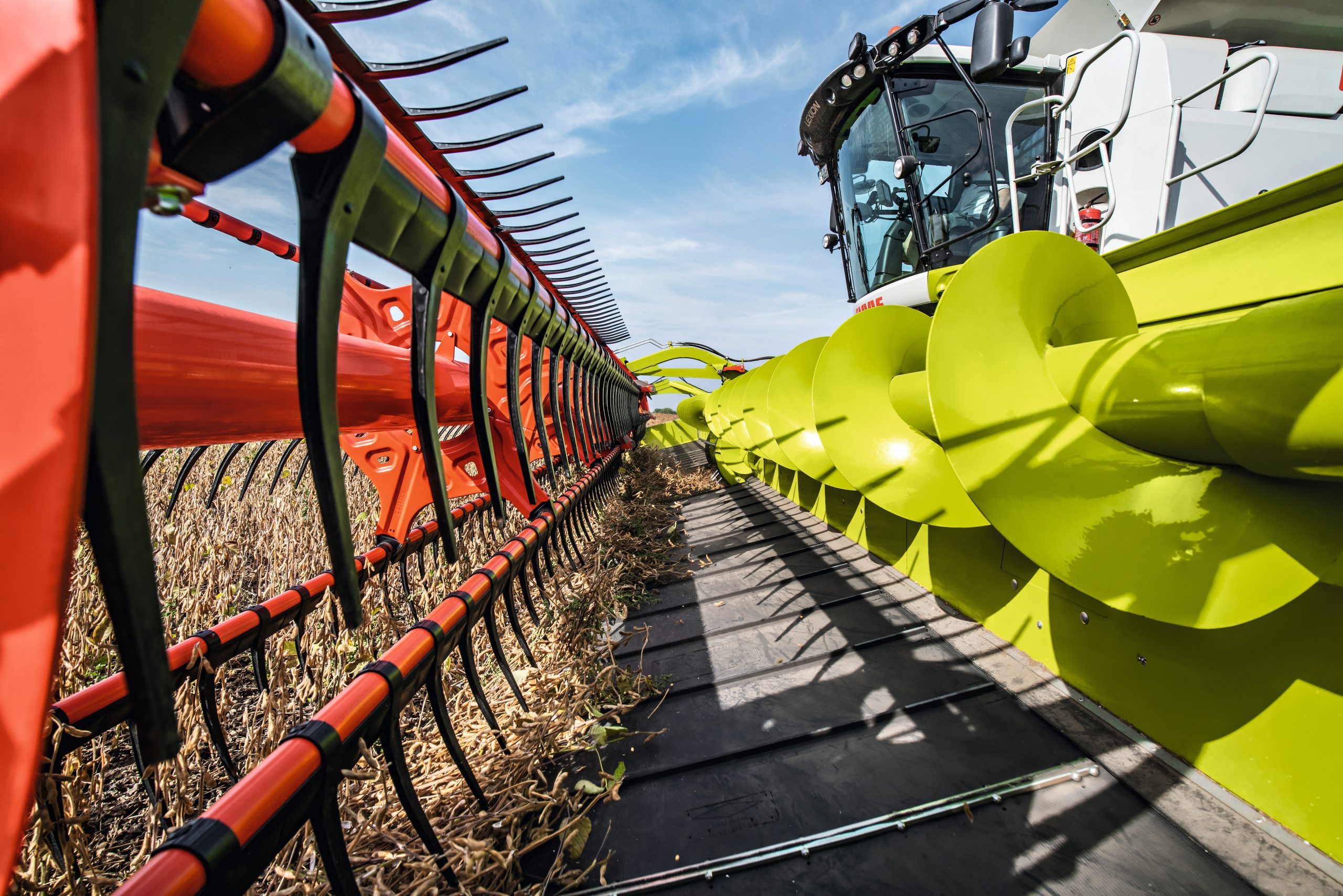
Accanto all’alimentazione regolare, non va scordata la versatilità. Che è unanimemente considerata l’altro grande pregio delle barre a tappeti. Non soltanto per l’adattabilità a diversi prodotti – che è un fatto oggettivo – quanto perché, almeno in Italia, la maggior parte di queste testate è venduta in versione snodata o, come si dice un po’ impropriamente, flex. In altre parole, sono le barre flessibili – anche se sarebbe più giusto chiamarle articolate – che si usano per tagli rasoterra o quasi, tipici della soia e di alcune leguminose con palchi molto bassi. Una barra a tappeti articolata permette di raccogliere grano con buoni risultati e al tempo stesso anche soia. Grazie a un kit apposito, alcuni modelli possono poi essere adattati alla trebbiatura del colza, prodotto per il quale si userebbe, normalmente, un modello a fondo variabile. Ma il notevole spazio presente tra lama e canale elevatore, in alcune barre a tappeti, rende possibile raccogliere efficacemente anche questo prodotto. Soprattutto se si parla di cultivar moderne, non eccessivamente alte. Ecco, dunque, che con una sola testata si possono gestire cereali, oleaginose e leguminose più diffuse. Con una buona barra a tappeti articolata e lo spannocchiatore, quindi, si chiude il cerchio delle testate di raccolta, con meno complicazioni e meno spazio occupato nel capannone.
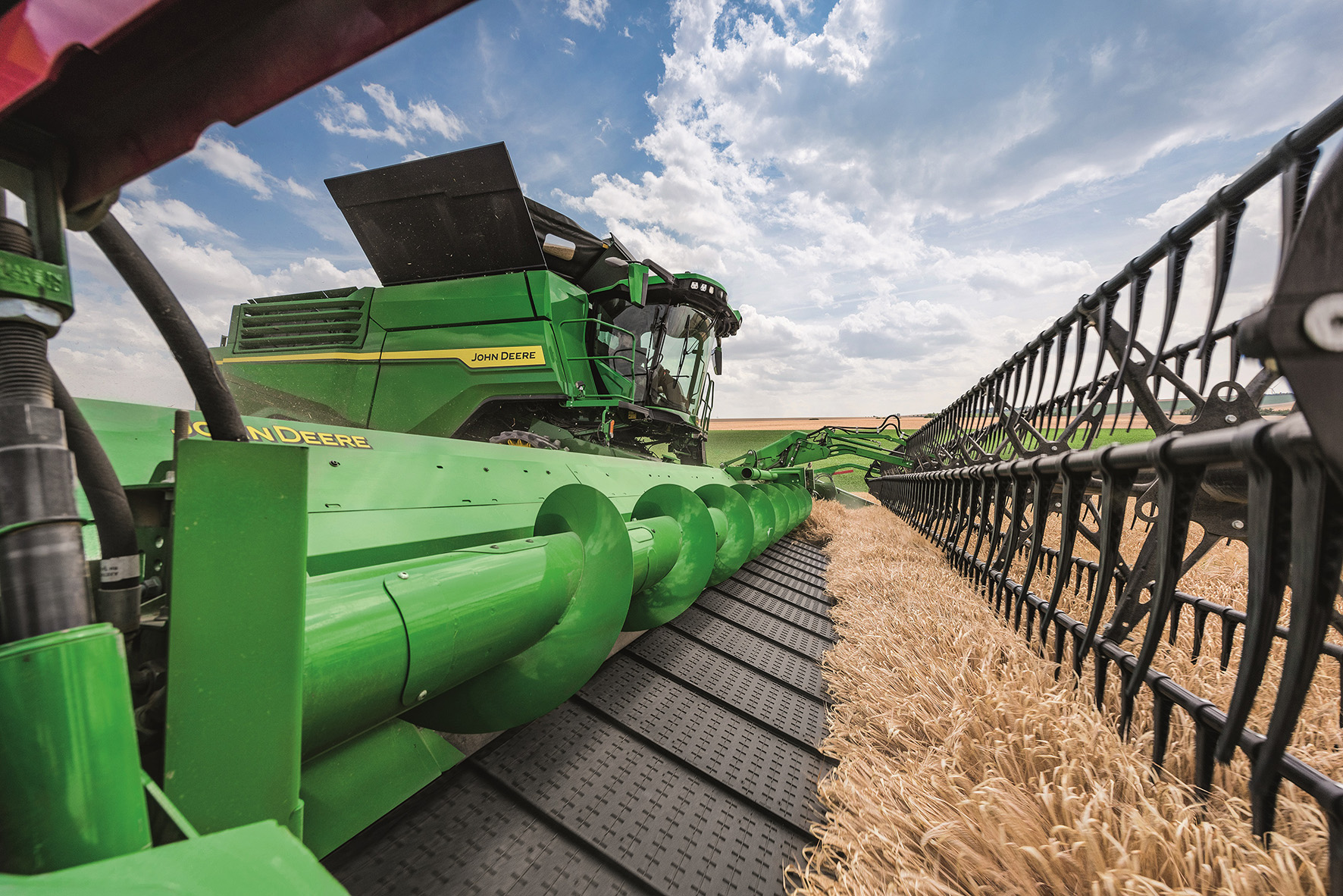
Più resa, ma più spesa
Non, però, con meno soldi. Il principale handicap della barra a tappeti è, senza dubbio, il costo. Unito a un peso ben superiore a quello di una normale barra da grano e a una maggior complessità costruttiva, da cui derivano maggiori necessità di manutenzione, anche giornaliera. Il prezzo, per queste macchine, è mediamente, del 25-30% più alto rispetto a una testata tradizionale, a parità di larghezza e costruttore. Del resto, tappeti, motori idraulici per azionarli, elettrovalvole, sistema di sospensioni, rulli eccetera hanno un costo. E anche un peso: è innegabile che queste testate siano più pesanti di una normale, composta da una lama, un po’ di lamiera, un aspo e una coclea. Servono dunque soldi per comperarle e un canale elevatore che non si lasci impressionare dai quintali in più che dovrà sollevare decine e decine di volte nella giornata.
In buona sostanza, abbiamo tracciato l’identikit di una macchina di alta potenza e prestazioni ed è infatti in abbinamento a esse che, principalmente, si acquistano barre a tappeti. Anche per la loro dimensione: essendo attrezzi pensati negli Stati Uniti, hanno infatti larghezze importanti – trovarne da 6 metri, per esempio, è quasi impossibile – e dunque richiedono una certa capacità di trebbiatura per lavorare al meglio. D’altra parte, una testata così costosa si giustifica soltanto se fa aumentare le prestazioni di una macchina molto performante, in modo che la maggior velocità di raccolta possa ammortizzare in tempi ragionevoli un prezzo che supera quello delle barre normali di quasi un terzo.

La domanda è allora se le barre a tappeti – che abbiamo visto essere più versatili e più uniformi nell’alimentazione – facciano anche aumentare la produttività, a parità di altri fattori. La risposta sembra essere positiva e legata soprattutto all’uniformità con cui il materiale arriva agli organi di separazione. Se questi lavorano in modo costante, senza picchi o momenti vuoti, ne beneficiano trasmissione e ingranaggi, senza dubbio, ma anche la resa oraria, che diventa molto più costante e, tendenzialmente, superiore. Secondo un test effettuato da Claas, nello stesso terreno e con la stessa macchina una barra a tappeti arriva a garantire 1 chilometro all’ora in più. La maggior produttività, alla luce di ciò, varia ovviamente a seconda della velocità di lavoro della barra standard, ma si può ragionevolmente fissare attorno al 20%. Valore che sale nettamente in caso di prodotti allettati. Grazie alla capacità di raccogliere a pochi centimetri da terra, le barre a tappeti, in particolare articolate, quando lavorano su cereali allettati hanno indubbiamente una marcia in più. Infine, con queste soluzioni, secondo Claas, si ottengono anche benefici sui consumi di gasolio, nell’ordine del 5-10%.
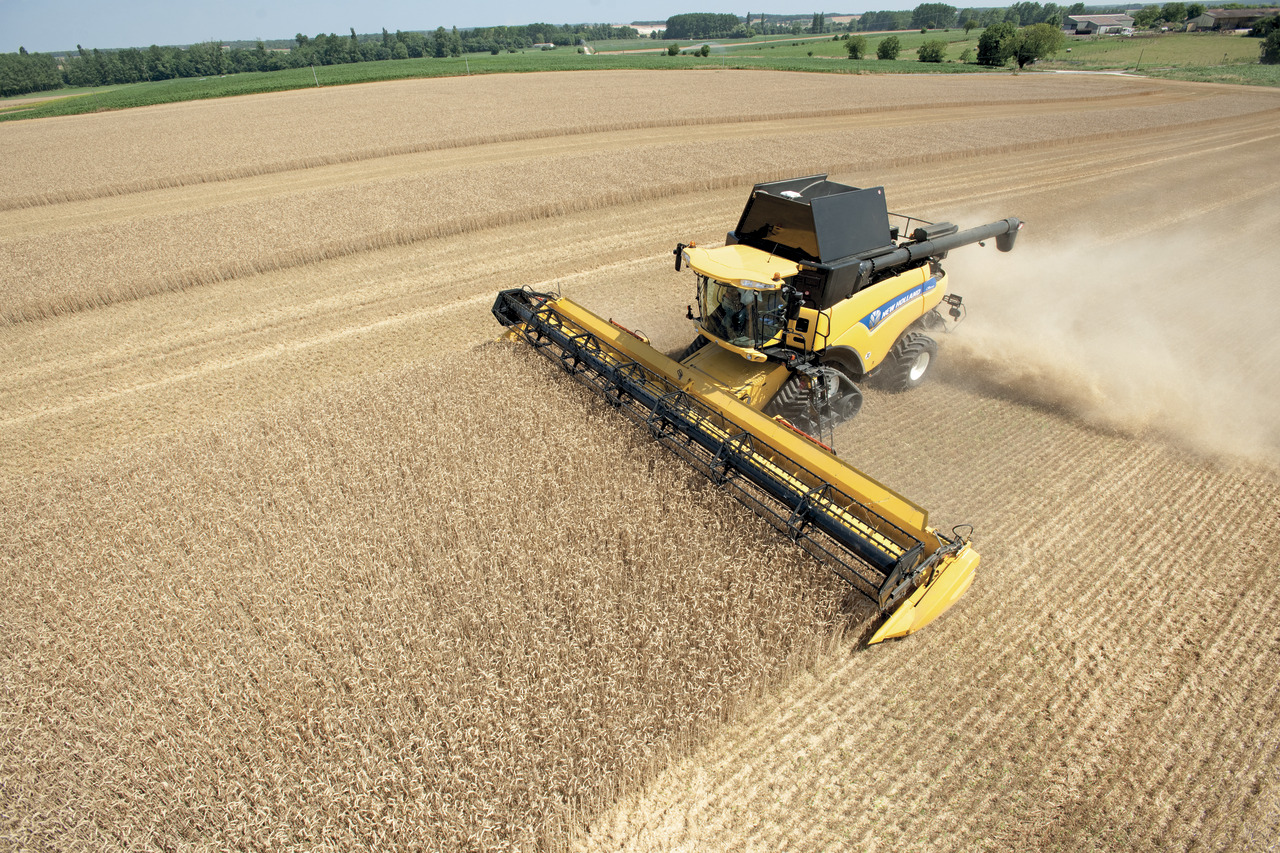
Panoramica costruttori
Visto l’interesse mostrato dai clienti e i buoni margini realizzabili dalla vendita, non stupisce che praticamente tutti i costruttori abbiano barre a tappeti nei loro listini. Con l’eccezione di Fendt, che al momento non dispone di una simile soluzione per le sue mietitrebbie, ma di una testata dotata sì di tappeti, però che scorrono dalla lama verso la coclea, a cui resta demandato il trasporto del prodotto al canale elevatore. Una soluzione ibrida, se vogliamo, con dimensioni fino a 40 piedi (12,2 metri) chiaramente adatta alle Ideal. Da quanto si apprende, sarebbe comunque allo studio una barra a tappeti vera e propria. Pronta, immaginiamo, per la prossima Agritechnica.
Non ha più una barra a tappeti in senso stretto nemmeno il gruppo Cnh, che per queste testate ha infatti stretto un accordo con Mac Don, uno dei leader mondiali di questa tecnologia, abbandonando in parallelo la produzione delle proprie barre a tappeti. Oggi, dunque, chi acquista New Holland o Case IH si vede consegnare in abbinamento una testata a tappeti Mac Don, ma con i colori del marchio prescelto e una dimensione compresa tra 7,5 e 15,2 metri (50 piedi).
Claas continua invece a produrre in casa le proprie testate, comprese le Convio a tappeti, nella versione standard o Flex (articolata-flessibile). Queste barre, che per l’Italia vanno da un minimo di 7,7 a un massimo di 9,3 metri (30 piedi), sono disponibili anche in allestimento riso, con aspo a otto barre e una maggior coppia. Stando a Claas Italia, le province risicole chiedono principalmente Convio rigide, mentre in Veneto optano per le flessibili, vista la forte presenza di soia. Lo stesso vale per il Ferrarese, nonostante in questa provincia il riso sia decisamente più diffuso della soia.
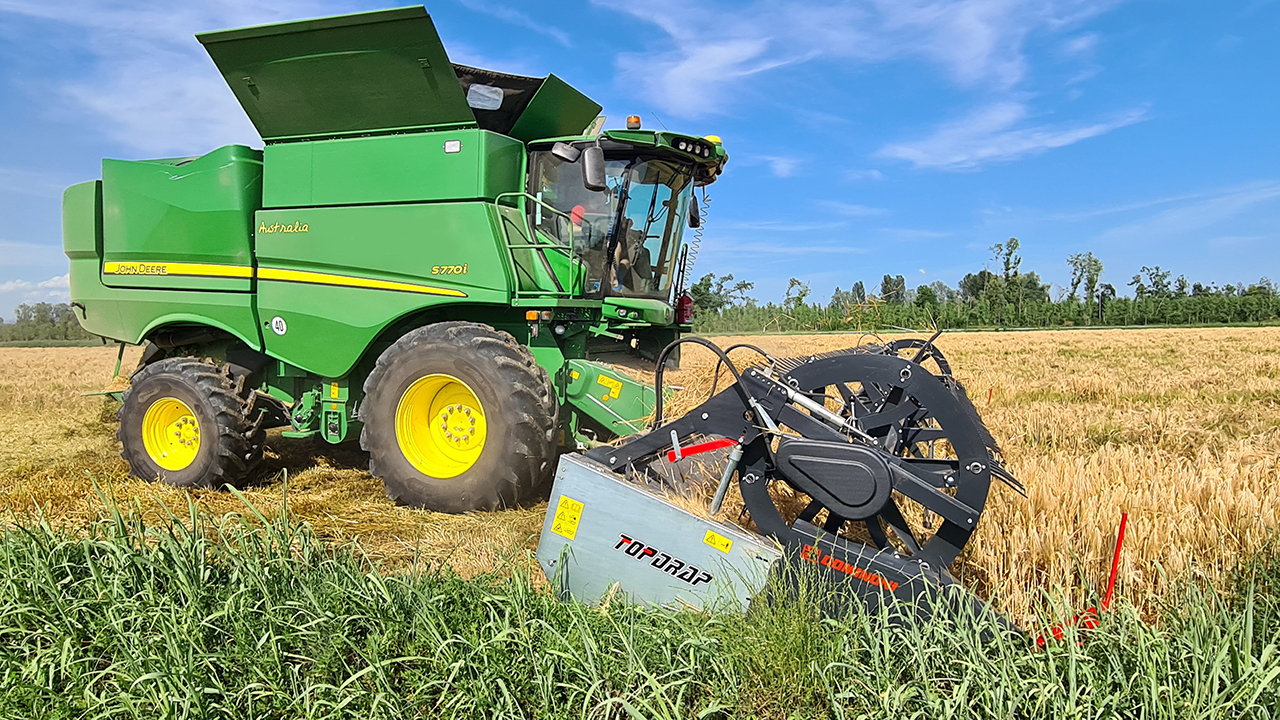
Per chiudere la panoramica sui costruttori di mietitrebbie, ricordiamo che anche John Deere offre testate a tappeti flessibili, grazie alla tecnologia HydraFlex. Sono distinguibili per la sigla Rdf e hanno larghezza fino a 45 piedi. A esse si aggiungono le barre Hdx, con tappeti da 1,2 metri di profondità, sufficienti a renderle adatte anche per la raccolta del colza.
Chiudiamo dando un’occhiata ai costruttori specializzati in testate. Abbiamo già citata la statunitense Mac Don, che oltre a vendere barre con il proprio marchio è diventata fornitrice di Cnh. Tra i marchi italiani, a quanto ci risulta, soltanto Dominoni ha in listino, al momento, una barra a tappeti. È la Top Drap, prodotta in due misure: 25 e 32 piedi (7,4 e 9,4 metri), mentre gli altri costruttori si sono piuttosto orientati sulle barre pieghevoli, che hanno il grande pregio di non richiedere un trattore al seguito per i trasferimenti.