Con il Green Deal europeo, la Commissione Europea sta per adottare un pacchetto di proposte atte ridurre in modo significativo le emissioni di CO2 al fine di limitare gli effetti del cambiamento climatico. Questa spinta ha portato i motori endotermici ad essere sotto i riflettori a causa della loro dipendenza dai combustibili fossili, tanto che la Commissione Europea sta addirittura attuando una transizione verso la mobilità elettrica. Questa transizione sta spingendo anche i costruttori di trattori a studiare soluzioni con minori emissioni di CO2 e infatti nelle ultime edizioni dell’Eima e di Agritechnica, sono state presentate soluzioni tecniche molto interessanti come, ad esempio, il Fendt e100 (foto 1) o il New Holland T6 Methan Power (foto 2). Benché sia tecnicamente possibile il passaggio verso autoveicoli elettrici, per le macchine agricole la strada è ancora lunga perché il passaggio verso queste soluzioni richiede una infrastruttura a supporto della transizione.
Considerando la pressione della Commissione Europea verso soluzioni con minori emissioni di CO2 e il costo sempre crescente dei carburanti, è necessario che gli agricoltori siano sempre più attenti agli sprechi dei carburanti al fine di ridurre le spese di gestione per la meccanizzazione. Uno di questi sprechi è dato dall’abitudine di lasciare il trattore fermo col motore al minimo. In questa condizione operativa, il motore non eroga alcun lavoro utile perché sia la frizione della trasmissione che quella della presa di potenza sono disinnestate. Molto spesso, gli agricoltori trascurano il consumo di carburante in questa condizione operativa visto che esso è molto minore del consumo durante una lavorazione. A titolo d’esempio, un trattore che durante le lavorazioni a piena potenza consuma 35 litri all’ora, al minimo ne consuma solo 3. Tuttavia, il carico motore al minimo è molto basso e quindi lo è anche l’efficienza del motore.
Non solo incuranza
Sulla base di una ricerca svolta dall’Università di Bologna insieme al gruppo CNHi, i trattori sono in sosta al minimo tra il 13 e il 43% del tempo e in media un trattore è al minimo per il 22% del tempo. Questi valori sono troppo elevati per essere dovuti soltanto all’incuranza degli agricoltori. Infatti, spesso gli agricoltori lasciano il motore al minimo a causa di alcune attività, come ad esempio il cambio attrezzo. In questa operazione, l’operatore deve mantenere il motore acceso al minimo per l’azionamento del sollevatore o della presa di potenza. In tali circostanze, spegnere il motore sarebbe poco pratico perchè allungherebbe il tempo dell’operazione. Tuttavia, in molte situazioni il motore viene lasciato al minimo per disattenzione dell’operatore, in quanto non richiede l’uso di sottosistemi come, ad esempio, il sollevatore o i distributori ausiliari.
In tali circostanze, spegnere il motore può essere conveniente soprattutto se la sosta è sufficientemente lunga. Tuttavia, per accendere un motore è richiesta una certa energia per accelerarlo fino al regime di minimo. Questa energia è in parte utilizzata dal motorino di avviamento, quindi prelevata dalla batteria, e in parte sotto forma di carburante iniettato in camera di combustione. L’energia elettrica utilizzata durante l’avviamento viene poi rigenerata dall’alternatore durante il funzionamento del motore, incrementando leggermente il consumo di carburante nei primi minuti di funzionamento dopo l’accensione. Pertanto, per soste molto corte, è probabilmente conveniente lasciare il motore al minimo piuttosto che spegnerlo per poi riaccenderlo.
Test su 4 trattori
Alla luce di ciò, all’Università di Bologna è stato svolto uno studio dove si è indagata la durata minima della sosta che apporta benefici in termini di consumi di carburante. A tal fine, sono stati svolti dei test di avviamento su quattro trattori equipaggiati con motori di diverse cilindrate. Nello specifico: Steyr Kompact 4095, Case IH Maxxum 115, New Holland T7.260 e New Holland T8.430 (foto 3). Durante i test di avviamento, è stato misurato l’assorbimento elettrico del motorino di avviamento e la quantità di carburate iniettata in camera di combustione. In questo modo è stato possibile misurare l’energia elettrica spesa per l’avviamento, convertirla in carburante (utilizzando gli opportuni rendimenti del motorino elettrico, dell’alternatore e del motore endotermico) e sommarla al carburante iniettato durante l’avviamento per stimare il carburante totale speso per avviare il motore (Fig. 1).
Dai test è emerso che per avviare un motore sono richiesti da 1,3 a 7,6 ml di carburante e, naturalmente, la quantità di carburante è crescente con la cilindrata del motore. La maggior parte del carburante è speso durante la fase dell’iniezione e non durante il funzionamento del motore per ricaricare la batteria. Il carburante speso per l’avviamento è stato confrontato con il consumo del motore al minimo e questo ha permesso di determinare che per soste di durata superiore a 5 secondi, è conveniente spegnere il motore piuttosto che lasciarlo al minimo. Tale durata è grosso modo indipendente dalla cilindrata del motore evidenziando che il consumo al minimo e quello necessario per l’avviamento sono grossomodo proporzionali tra loro. Un valore così basso della durata minima della sosta rende sempre conveniente spegnere il motore ogni qualvolta l’operatore lascia la cabina.
Quanto carburante si spreca
Al fine di valutare gli effettivi benefici percepiti dall’operatore, si è calcolata la quantità di carburante che gli agricoltori potrebbero sprecare perché non spengono il trattore quando serve. A tal fine, i trattori usati per i test di avviamento sono stati monitorati per diversi mesi installando su ciascuno di esso delle scatole nere per registrarne l’impiego. In particolar modo è stato monitorato l’uso dei diversi sottosistemi e quindi del motore, sollevatore, distributori, cambio, ecc. Il processo di registrazione non era visibile agli operatori in modo da non interferire con le attività agricole e da registrare i dati più realistici possibile. In totale, sono state registrate circa 4mila ore di utilizzo complessivo tra tutti i trattori. Dai dati raccolti è stato possibile determinare il numero e la durata delle soste (Fig. 1) e per ciascuna sosta è stato possibile determinare se queste fossero necessarie oppure no.
In particolar modo, ciascuna sosta è stata classificata come necessaria, se è stato utilizzato un qualche sottosistema; altrimenti, è stata classificata come non necessaria. Quindi, se durante una sosta è stato rilevato l’uso del sollevatore, attraverso la rilevazione della variazione della sua posizione, la sosta è stata classificata come necessaria (Fig. 2).
I trattori hanno operato al minimo tra il 10% e il 31% del tempo. La percentuale più bassa è stata registrata per il New Holland T8, probabilmente a causa del fatto che questo trattore è stato prevalentemente utilizzato per lavorazioni pesanti su grandi appezzamenti, dove i tempi morti sono solitamente bassi. La percentuale più alta, invece, è stata registrata per il Case IH, il quale è stato utilizzato principalmente per trasporti e operazioni di sfalcio. Per una quota che va dal 50 al 77% del tempo totale di sosta, gli operatori non hanno utilizzato alcun sottosistema, evidenziando che la maggior parte delle soste erano non necessarie. Per i quattro trattori, le durate medie delle soste classificate come non necessarie erano comprese tra 85 e 200 secondi. Questi valori sono ben superiori ai 5 secondi registrati duranti le prove di avviamento, evidenziando la convenienza nello spegnere il motore nelle soste non necessarie.
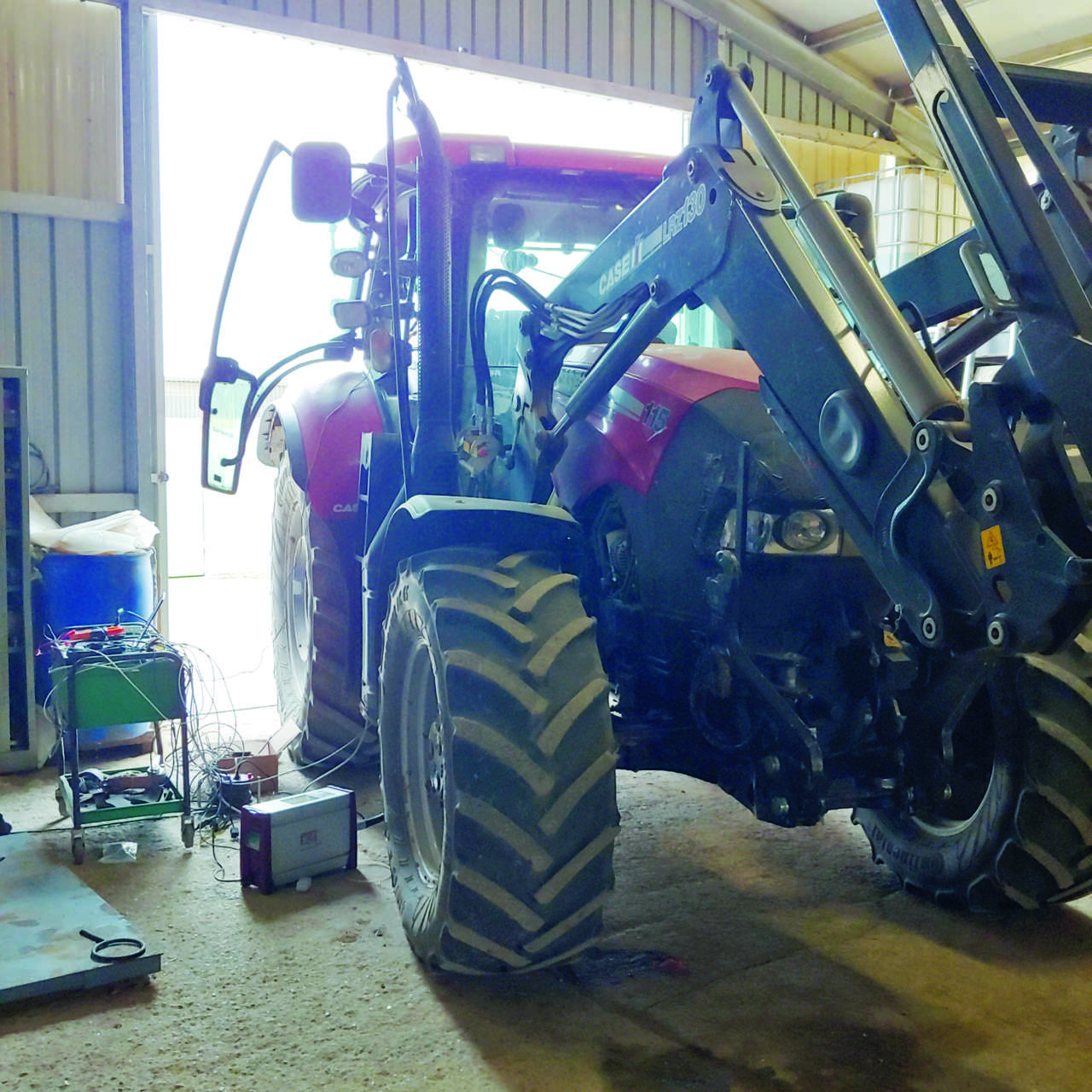
Margini di miglioramento
In queste soste, è stato ipotizzato che il motore venisse spento e che questo venisse riavviato al termine della sosta. Per ciascuna sosta è stato calcolato il risparmio di carburante includendo anche il carburante speso per l’avviamento. Il risparmio di carburante stimato su questi trattori è compreso tra l’1,1% per il New Holland T8 e il 5,1% per il Case IH. Queste percentuali sono molto variabili perché dipendono non solo dal tempo in cui il trattore è lasciato al minimo, ma anche dalla severità di utilizzo nelle condizioni di lavoro. Ad esempio, il New Holland T8 è stato utilizzato a lungo per le lavorazioni pesanti e quindi molto energivore, dove è basso il contributo del carburante speso durante le soste rispetto al totale. Il Case IH, invece, ha presentato i benefici maggiori perché è stato utilizzato principalmente per lavorazioni leggere e quindi il contributo di carburante speso durante le soste sul totale era maggiore. Naturalmente, lo spegnimento del motore può comportare un maggiore stress per la batteria e il motorino dell’avviamento, dato che il numero degli avviamenti raddoppierebbe. Tuttavia, può anche portare a un minore stress per altri componenti come, ad esempio, per il motore e l’alternatore, che sono sottoposti a un minor numero di giri, ma anche per il filtro antiparticolato. In termini di risparmio economico, è stato registrato un valore compreso tra i 15 e i 40 litri di carburante ogni 100 ore di utilizzo. Sicuramente un risparmio non marginale in un settore dove i margini sono sempre più risicati.
Si ritiene che per risparmiare carburante sia necessario avere motori nuovi ed efficienti. In realtà molto spesso ci sono margini di miglioramento nascosti e uno di questi è sicuramente non lasciare inutilmente il motore al minimo.
I benefici registrati in questo studio potrebbero essere raggiunti solo con un sistema di tipo start-and-stop come quello adottato nelle moderne automobili. Un sistema del genere, che riaccende il motore ogniqualvolta è richiesto l’uso di un qualche sottosistema, permetterebbe non solo di risparmiare carburante, ma anche di migliorare il comfort degli agricoltori quando si trovano a svolgere le operazioni di manutenzione all’esterno del trattore. Tuttavia, al fine di migliorare la funzionalità del sistema, sarebbe anche utile elettrificare l'impianto di aria condizionata al fine di mantenere in temperatura la cabina anche quando il motore è spento.